About Us
We unlock the power of data for public good
GovEx supports and coaches leaders and their teams to build a data-driven public sector that fairly and justly uses data, research, and analytics to better understand complex issues, engage residents, and implement policy interventions that lead to equitable outcomes and transform the standard of living for underserved residents.
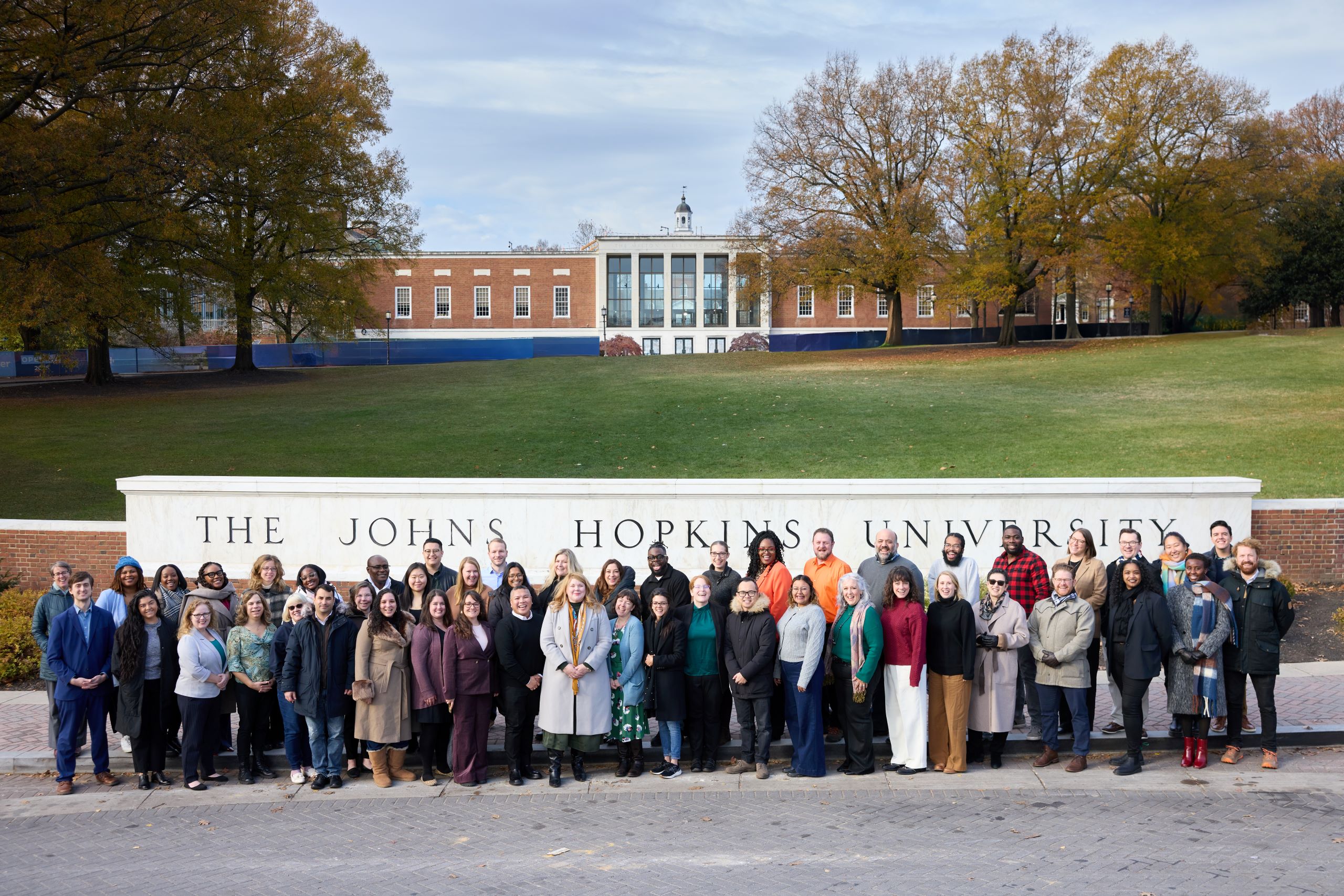
Who We Are
The GovEx team comprises some of the foremost thinkers on data use in the public sector in the world, including many former government officials now working alongside the public sector to help them develop better technology policies and embrace the positive benefits of that technology all over the globe.
What We Do
GovEx works with cities in three key ways.
Field-Defining Research: GovEx provides rapid-response tools and analysis to help cities address emerging challenges.
Expert Advisors: GovEx is led by former government practitioners with academic grounding to share best practices and training.
Public Sector Connectors: GovEx convenes city leaders and the world’s foremost data thinkers to identify cutting-edge solutions.
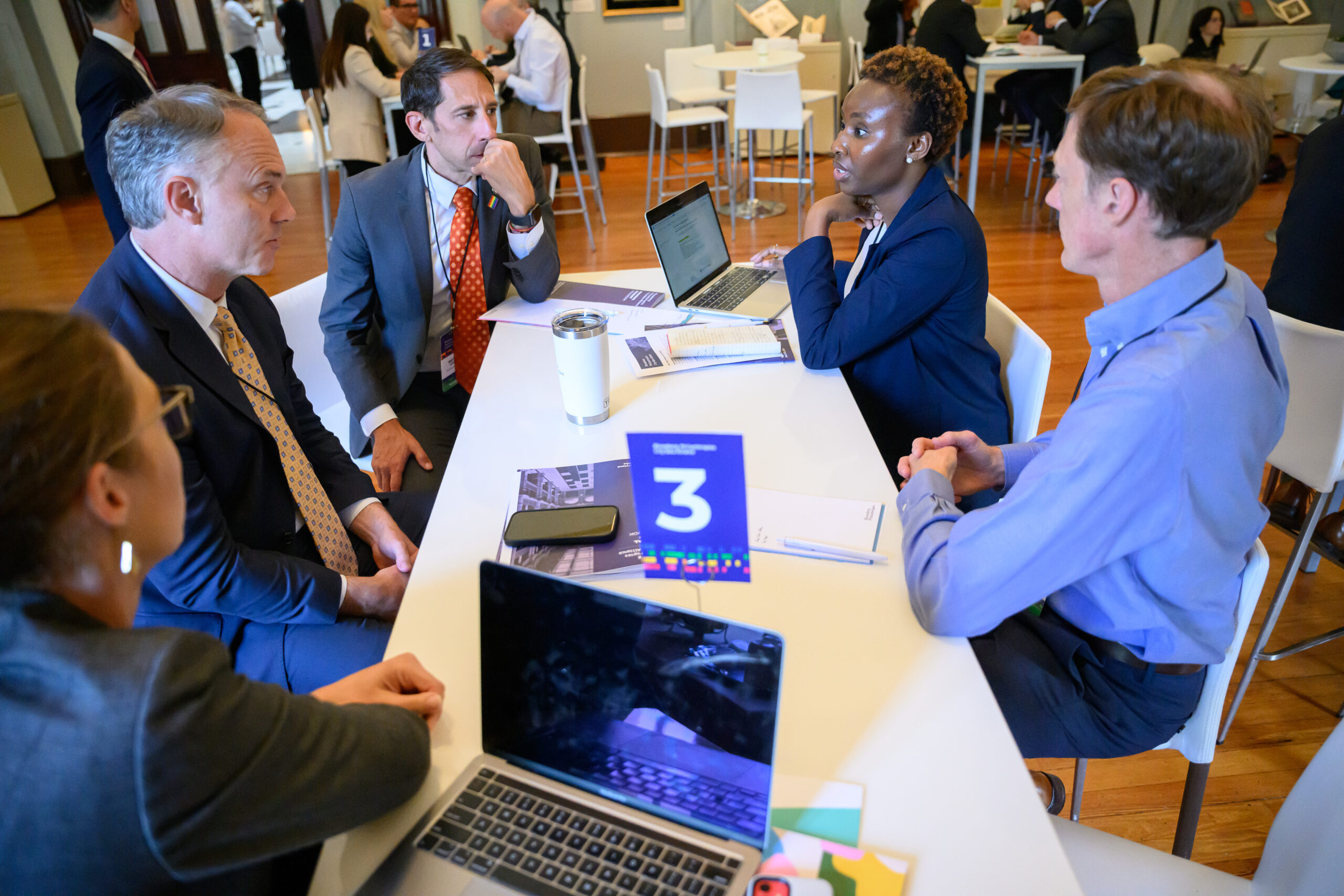